Revitalising Power Plants: How Retrofitting Boosts Efficiency and Cuts Costs
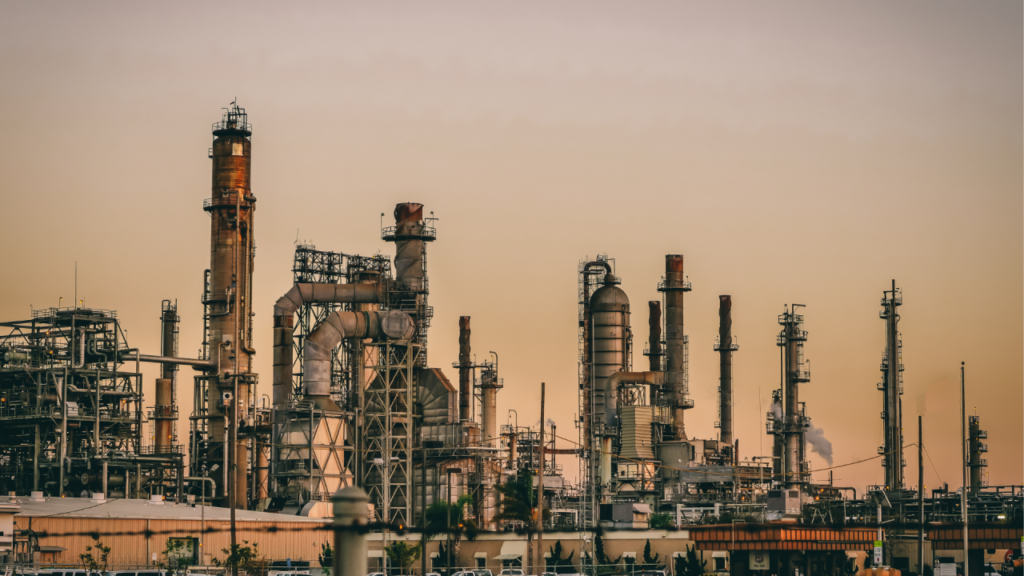
Conventional power plants today face mounting pressure to deliver better performance, consume less fuel, and reduce emissions—all without expensive rebuilds or extended downtime. Retrofitting offers a practical solution, enabling plant operators to improve efficiency, extend the lifespan of their facilities, and stay competitive in an evolving energy landscape.
Why Focus on Efficiency?
Efficiency is more than a buzzword—it’s the cornerstone of reliable and cost-effective power generation. Retrofitting transforms older plants into smarter, more productive systems that use existing assets to meet modern demands.
Why Retrofitting for Efficiency Matters:
Improved Output: Enhanced performance enables plants to meet growing energy demands without requiring additional infrastructure.
Cost Savings: Lower fuel consumption and reduced maintenance needs translate to long-term operational savings.
Longer Life: Upgrades help extend the operational life of power plants, delaying costly replacements and reducing capital expenditure.
Key Efficiency Upgrades for Power Plants
1. Turbine Upgrades
Aging turbines often underperform, wasting valuable energy. Replacing or refurbishing them with modern, high-efficiency models extracts more energy from the same amount of fuel. For gas and steam turbines alike, these upgrades can significantly improve overall plant output.
2. Heat Recovery Systems
Heat Recovery Steam Generators (HRSGs) capture waste heat from engines or gas turbines and convert it into usable energy. This upgrade not only enhances plant efficiency but also reduces fuel dependency. HRSG retrofits are particularly beneficial for plants operating gas turbines or reciprocating engines.
3. Boiler Optimisation
Older boilers are prone to inefficiencies, leading to significant energy losses. Modernising boilers with advanced controls, burners, and insulation improves fuel-to-energy conversion and reduces unnecessary waste.
4. Advanced Monitoring Tools
Digital tools such as SCADA systems and predictive maintenance software provide operators with real-time insights into plant operations. These tools help detect inefficiencies early and address potential problems before they escalate, reducing unplanned maintenance.
5. Improved Cooling Systems
Cooling systems often consume significant energy. Retrofitting with advanced technologies like variable-speed drives or more efficient heat exchangers reduces energy requirements, freeing up capacity for power generation.
Common Challenges in Retrofitting
While retrofitting brings immense benefits, it does come with its share of challenges:
Compatibility Issues: Upgraded components must integrate seamlessly with older systems, sometimes requiring custom solutions.
Operational Downtime: Retrofits can disrupt operations temporarily, but phased implementation and proactive scheduling minimize this impact.
High Initial Costs: Although upfront investments can be significant, the long-term reductions in fuel and maintenance costs make retrofitting a cost-effective strategy.
How Retrofitting Improves Operations
Retrofitting is not just about updating equipment; it’s an opportunity to fundamentally enhance plant performance:
Lower Maintenance Costs: Modern systems are more reliable and require less frequent servicing, reducing repair expenses.
Faster Response Times: Upgraded equipment adapts more quickly to fluctuations in demand, improving grid reliability.
Reduced Emissions: By optimising fuel use, retrofitted plants emit fewer greenhouse gases without requiring additional emission control technologies.
A Step-by-Step Approach to Retrofitting for Efficiency
Assess the Plant Perform a detailed analysis of the plant’s existing systems to pinpoint inefficiencies and identify areas for improvement.
Set Efficiency Goals Define clear objectives—such as reducing fuel use, increasing output, or cutting operational costs—to guide the retrofitting process.
Select Upgrades Focus on upgrades like turbines, HRSGs, and digital monitoring tools that deliver the highest returns.
Plan for Downtime Develop a phased approach to minimise interruptions during upgrades. This reduces surprise maintenance and ensures smoother operations.
Monitor Post-Retrofit Performance Use digital tools to track the effectiveness of upgrades and identify additional areas for improvement over time.
Retrofitting in Action: Proven Results
Examples from the field highlight the tangible benefits of retrofitting:
Upgraded Turbines: A coal plant that upgraded its turbines achieved a 15% increase in output while cutting fuel consumption by 10%.
Heat Recovery Systems: Adding an HRSG to an ageing gas-fired plant saved millions annually in operating costs by capturing waste heat.
These examples illustrate how targeted retrofits can yield significant gains in both performance and cost savings.
The Future of Retrofitting
Retrofitting isn’t just a short-term fix—it’s a forward-looking strategy. By enhancing efficiency, operators can meet growing energy demand, cut costs, and keep conventional power plants competitive in a market that demands constant improvement.
Ready to Retrofit?
If your power plant isn’t performing to its full potential, retrofitting could be the answer. Let’s work together to explore efficiency upgrades tailored to your operations, helping you get the most out of your existing assets. Contact us today to start the conversation.